Cleaning system: | spray cleaning with fan nozzles |
Functional principle: | turntable with multiple treatment zones and rotating nozzle systems |
Number of tanks: | single and multiple tank systems |
Loading: | front loading and unloading in the same position |
Housing: | stainless steel |
Tank insulation: | stainless steel |
Tankisolierung: | Edelstahl |
Control and operation: | Siemens Simatic with Siemens touch panel |
Bath monitoring: | Libelle Fluid Control |

Intelligent cleaning with BvL apps and digital networking!
Transparent process information for predictive diagnostics and maintenance of the system: efficient and automatic.
Depending on requirements, the TwisterRT rotary indexing table is equipped with individual options. Number and type of the different processing stations for cleaning and drying are selected based on the requirements at hand. Depending on size, geometry and weight of the component, the washing and drying systems are designed to ensure that even hard-to-reach areas will be treated.
Integration into your production
The TwisterRT can be integrated into production lines and robot cells. Manual loading is also possible.
- optimum part cleanliness for a greater process reliability
- compact cleaning solution with low space requirements
- simple to implement in robot cells and production lines
- automated or manual feed
- loading/unloading in the same position
- for large quantities and short cycle times
- can be combined with high-pressure/lance technology
Technology in detail
Cleaning technology
- circular treatment zone layout
- rotating platform for mounting and moving the parts
- spray cleaning with vertically rotating nozzle system
- 360° part cleaning with special nozzle system
- simultaneous treatment of the parts in one working chamber
- nozzles and nozzle frames can be adapted to the part
- working dimensions, load capacities and pump capacities can be adapted
Process steps
Parts proceed through the process steps within a chamber in various treatment zones
- washing, rinsing (optinoal), drying (optional)
- the treatment zones can be adapted individually
Options and extensions
- high-performance drying system, designed for complex part geometries
- increased pump capacity
- bath maintenance options
- process reliability: Libelle Cleaner Control, Libelle Oil Control, Libelle Data Control, remote diagnosis
- cascade guiding
- handling systems: gantry cells, robots
- floor drip tray
- can be combined with high-pressure/lance technology
- other system components
Impressions of individual configurations
The TwisterRT rotary cycle system can be customized to meet individual requirements. The number and type of the different treatment stations for cleaning and drying are configured to meet the requirements at hand.
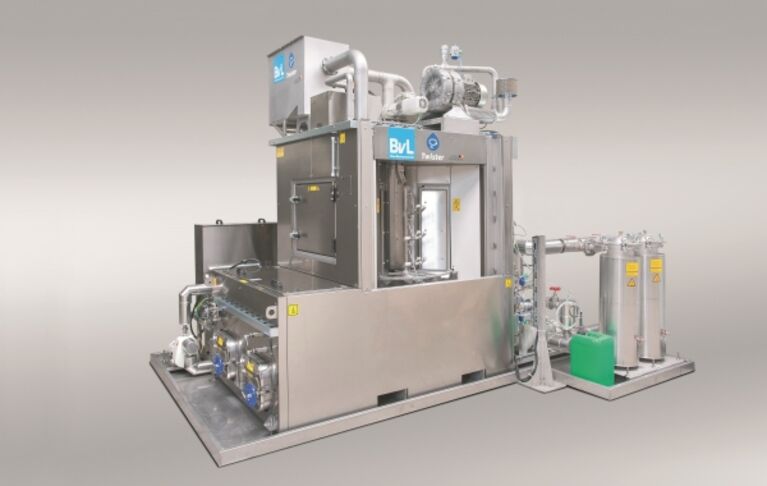