Automated component cleaning frees up staff capacity and ensures process reliability
Solution in times of skills shortage: loading with gantry handling and automated unloading
Component manufacturers have been focusing increasingly on cleaning processes in recent years. A reliable, durable end product that functions with repeat accuracy requires perfectly cleaned components.
Tackling the current skills shortage with automation
In addition to the increasing cleanliness requirements, staff costs also have to be factored in. Optimum integration of component cleaning into the production process requires basic cleaning as well as consideration of the component handling systems and the transport into and through the cleaning system. One of the objectives is to reduce the staff required for the handling processes. This aspect is currently of particular importance because the lack of skilled personnel is becoming increasingly evident in mechanical engineering as well. The skills shortage has been discussed for a while, but it is now becoming a serious issue. The baby boomer generation are retiring, and the number of junior staff is significantly lower.
Automation options for component cleaning
The solution for freeing up staff can be very simple: automation. That is exactly where BvL comes in – with a number of options for running a cleaning system unattended. Some examples here are automated roller conveyors with feed and discharge of baskets, fully automated gantry solutions, robot loading, tripods, flexible conveyor belts, chain conveyors, etc.
Interface coordination for reliable processes
A smooth production process requires reliable coordination and alignment of mechanical, electrical and “cold” hardware and software interfaces. BvL Oberflächentechnik GmbH have already implemented numerous projects in this field in recent years and have specialist knowledge of how to integrate the cleaning systems into the production process. BvL cleaning systems fit seamlessly into the production flow and are perfectly coordinated with the linked conveyor technology. The design of the cleaning system is determined by the customer’s processes – whether as an island solution or as an in-line solution.
As one of the market leaders for water-based component cleaning systems, BvL Oberflächentechnik GmbH has permanently optimized its product range to meet the high cleanliness requirements. BvL can offer a suitable cleaning system for any application – from general component cleaning on the outside to targeted cleaning inside of parts, e.g. cooling channels, blind holes, undercuts.
Example of automated, unattended operation of the Niagara basket washing system with gantry loader
A manufacturer of drive components for agricultural machinery produces shafts, gearwheels and housings with a large number of machining stations. The production department decided to transport the parts from one machining step to the next in basket-like workpiece carrier racks. Several stackable racks are stacked on floor rollers and transported within the factory on a tugger train. The workpiece carriers are designed to protect parts against damage caused by impact and to guarantee plenty of clearance for spray or flood cleaning.
At the material station for the component cleaning system, the floor rollers with the racks park in bays underneath the loading portal. This is where the component cleaning system takes over. As soon as the cleaning system is clear, the gantry moves above the racks to be cleaned and transfers them to the automatic feed and discharge unit in front of the cleaning system.
The cleaning and drying programs of the BvL system are customized for the manufacturer’s workpiece carriers and the cleaning program runs based on the set parameters. In the meantime, the floor roller before the gripper is cleaned at a separate cleaning station and then placed on an unloading position. The cleaned workpiece carriers are stacked back onto the clean “tray” in front of the portal. When the stacking height has been reached, a traffic light releases the stack for onward transport, and the next processing step can start.
As a result, the component cleaning process requires no operating staff and the cleaning process is executed reliably and efficiently.
Contact:
BvL Oberflächentechnik GmbH
Grenzstr. 16
48488 Emsbüren
Germany
Tel.: +49 5903 951-60
Fax: +49 5903 951-90
info@bvl-group.de
www.bvl-group.de
Press release:
Christine Brühöfner
Marketing
Tel.: +49 5903 951-509
Fax: +49 5903 951-90
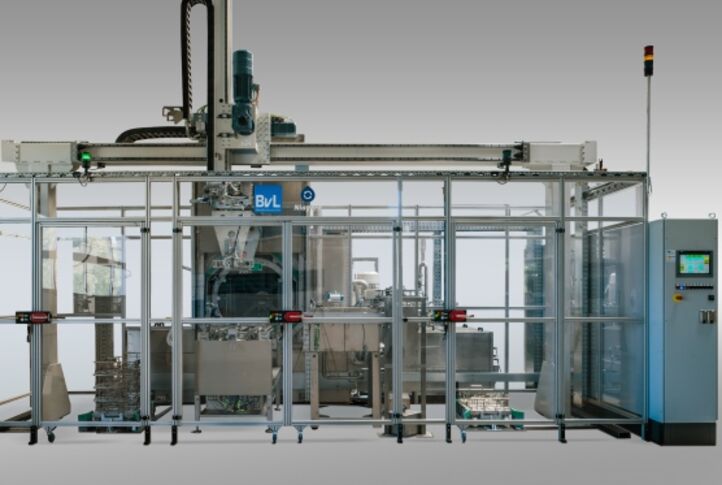