Cleaning tumble dryer drums with short cycle times
Tumble dryer drums must be thoroughly clean and spotlessly dry before they can be installed in the household appliances. Short cycle times for the cleaning system are important for achieving a high throughput.
Specific application:
The Polish factory of a world-renowned Group of companies in the field of household and industrial kitchen appliances chose a cleaning solutions from BvL Oberflächentechnik GmbH for this application. After the manufacturing process, the drums are soiled with traces of oil and grease. For installation into a clothes dryer, it is imperative that the drums have been thoroughly cleaned and are mostly stain-free. The BvL Yukon continuous cleaning system cleans and dries the tumble dryer drums thoroughly in a cycle time of only 12 seconds per part. The drums continuously move through the following sequential treatment zones of the cleaning system to ensure consistent material flow and high throughput. The plant operator can control the conveying speed to thus react flexibly.
Individually adapted cleaning system
When planning the system, BvL considered more than just the manufacturer’s specifications for quantity and time. The restricted space at the installation site also had to be taken into account in order to achieve optimum integration of the cleaning system into the production flow. As a result, the continuous system was equipped with a 180-degree corner transport system in this case and the cleaning zones were arranged parallel to the drying zone. A manual maintenance opening on the loading station makes the machine easily accessible for the operator from all sides.
Efficient cleaning technology
After automatic loading of the tumble dryer drums into the cleaning system, they are positioned automatically in the feed zone: A special system lowers the drums onto the workpiece holders. This ensures that the parts are in the optimum position for the subsequent cleaning process and prevents poor cleaning results due to incorrect positioning of the workpieces.
The drums then continuously move through the following sequential treatment zones of the system: They are cleaned thoroughly from all sides in the cleaning zone. The nozzle system is individually aligned for the specific parts. Before the drums move on to the rinsing zone, they are blasted with unheated air in an intermediate zone to prevent the cleaning media from mixing or spraying out between cleaning and rinsing. The parts are then blasted with air again before the drying process. In this case, this is done from above and underneath with a rotating air blast system that is also specifically tailored to the drums. The final drying of the drums takes place in the BvL Nevada drying zone by means of electrically heated air. After this step, the cleaned and dried drums can be removed from the roller conveyor in the discharge zone.
Saving energy with intelligent sensor technology
The Nevada drying system not only delivers consistent drying results, but also saves energy with intelligent sensor technology. Water and energy consumption are significantly reduced compared to a conventional drying system. The exhaust air management, for example, controls the fan based on the measured humidity, while the energy discharged in the form of hot exhaust air is kept to the necessary minimum. The optimised flow of the drying process also reduces the required heating input and therefore any unnecessary energy consumption. Of course, all tubes, filters and tank covers are insulated to reduce the loss of thermal energy in these areas.
Flexible adaptation to changed operational requirements in future
The cleaning system can be adapted to changed operational requirements at any time. The household manufacturer is well prepared for the future as upgrade options are available if the requirements for capacity and throughput should change over time.
BvL Oberflächentechnik GmbH is one of the largest suppliers of water-based industrial cleaning systems in Germany. As a system partner, BvL offers comprehensive customer solutions through integrated services – from compact washing units and filtration and automated solutions to complex large projects with process monitoring, always complemented by reliable service. BvL currently has around 160 employees. In terms of exports, the company has expanded its position on an international scale, and can rely on an extensive sales and service network in 20 countries.
Contact:
BvL Oberflächentechnik GmbH
Grenzstr. 16
48488 Emsbüren, Germany
Tel.: +49 5903 951-60
Fax: +49 5903 951-90
info@bvl-group.de
www.bvl-group.de
Press Release:
Christine Brühöfner
Marketing
Tel.: +49 5903 951-509
Fax: +49 5903 951-90
christine.bruehoefner@bvl-group.de
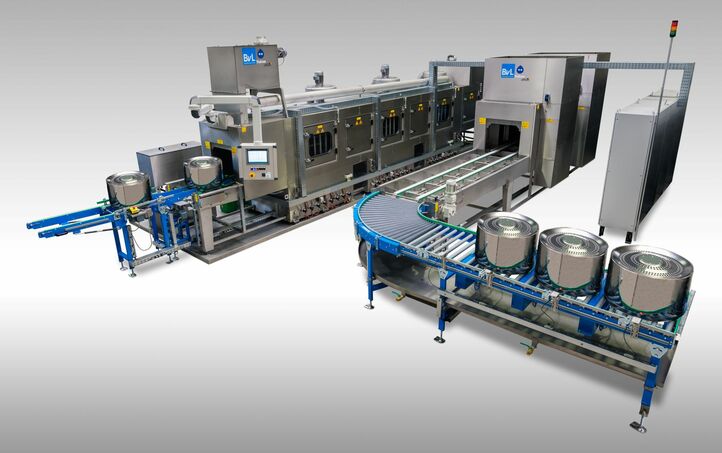
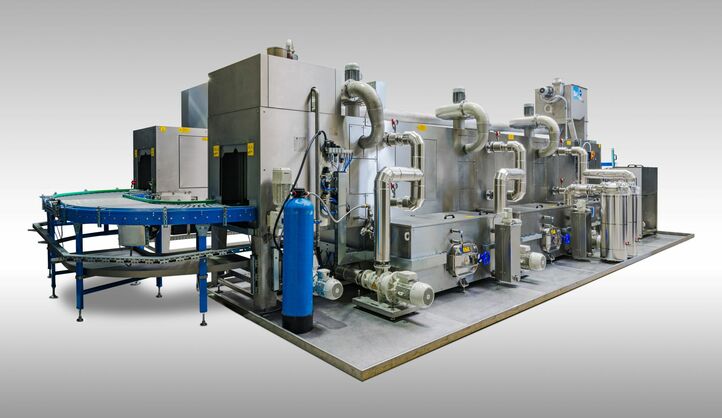
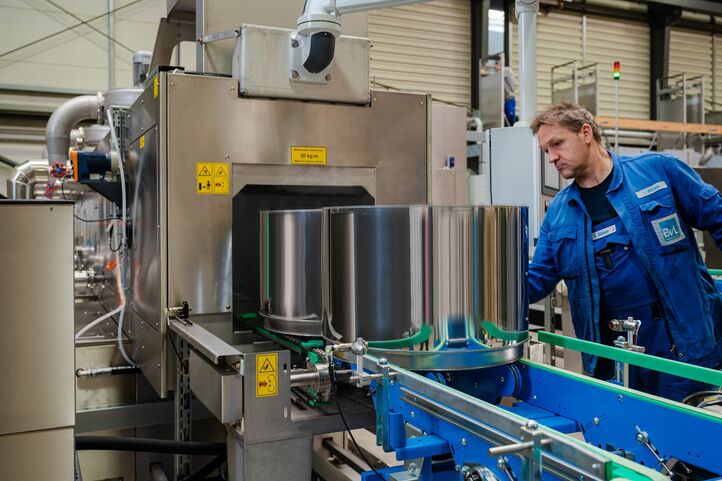