Easy yet powerful solution for parts cleaning
Medium-sized companies often need a standard system for parts cleaning that has to be easy to operate without compromising on cleaning performance.
The basket cleaning system is suitable for thorough, all-around cleaning of small parts in baskets (bulk goods) or individual parts on workpiece carriers. It offers uncomplicated handling and ensures fast work processes. The system uses flood/spray cleaning.
Thorough and uncomplicated parts cleaning – ideal for metal machining
A specific application from metal machining illustrates the requirements for an efficient standard cleaning solution. A medium-sized metalworking company from the German Saarland region chose a Niagara basket cleaning system from BvL Oberflächentechnik GmbH. It reliably and efficiently removes swarf, oil and emulsions from hydraulic blocks.
Thanks to the simple control of the machine with the intuitive touch panel, the plant operator does not need extensive training for the cleaning system. They can see at a glance, for example, whether the cleaning medium is still clean enough to ensure constant parts cleanliness. The Niagara cleaning system is equipped with the Libelle Fluid Control as standard – a sensor system that automatically measures the bath condition in the system. The Niagara requires little maintenance and all components of the cleaning system are easily accessible. It convinced the metalworking company with its robust design and high level of quality. The outer walls of the system are clad with insulated panels made of high-quality stainless steel plates. A thermal insulation layer between the inner and outer panels provides good thermal and sound insulation. The parts basket and the tool holder are also made of high-quality durable stainless steel.
Efficient cleaning of hydraulic blocks
The hydraulic blocks are pushed into the system in a parts basket.
All steps of the cleaning process, such as washing, rinsing, and drying are carried out in one space-saving chamber. A spray/flood process with aerowheel technology in combination with rotating parts baskets is used to achieve all-around thorough cleaning of the hydraulic blocks. In the Niagara standard system, the parts baskets rotate around a fixed nozzle system. After the spray process, the chamber is flooded. This ensures that all parts in the basket are cleaned thoroughly.
For this application, BvL adapted the nozzle system of the Niagara standard system for this customer: It is not installed permanently as in the standard, but rotates 360 degrees around the swiveling parts basket with the hydraulic blocks. One of the advantages is that the parts baskets can also be swiveled with only a very small angle if required. This can prevent the parts from being knocked together, which could cause damage. One essential benefit of this special process technology of counter-rotating/synchronized rotation of the parts basket and nozzle system, however, is that it ensures particularly intensive cleaning of the hydraulic blocks. It allows the cleaning medium to reach even into blind holes and release dirt particles. The subsequent rinsing and drying process steps are carried out in the same chamber.
After the cleaning process, the hydraulic components can be processed further without any problems or faults. The high cleanliness requirements in metal machining are met and a high level of product quality can be ensured.
Practical additions in cleaning technology
The comprehensive standard equipment of the BvL Niagara cleaning system can be individually adapted to customer requirements with additional equipment. The BvL expert team considers the customer’s entire production process. One example is that a roller conveyor can easily be used as the handling system for automatic loading and unloading instead of a charging trolley or cross-movement table. Other Smart Cleaning functions are possible for predictive maintenance. The BvL product portfolio covers many areas of application with different challenges and requirements of parts cleaning.
BvL Oberflächentechnik GmbH is one of the largest suppliers of water-based industrial cleaning systems in Germany. As a system partner, BvL offers comprehensive customer solutions through integrated services – from compact washing units and filtration and automated solutions to complex large projects with process monitoring, always complemented by reliable service. BvL currently has around 160 employees. In terms of exports, the company has expanded its position on an international scale, and can rely on an extensive sales and service network in 20 countries.
Contact:
BvL Oberflächentechnik GmbH
Grenzstr. 16
48488 Emsbüren, Germany
Tel.: +49 5903 951-60
Fax: +49 5903 951-90
info@bvl-group.de
www.bvl-group.de
Press Release:
Christine Brühöfner
Marketing
Tel.: +49 5903 951-509
Fax: +49 5903 951-90
christine.bruehoefner@bvl-group.de
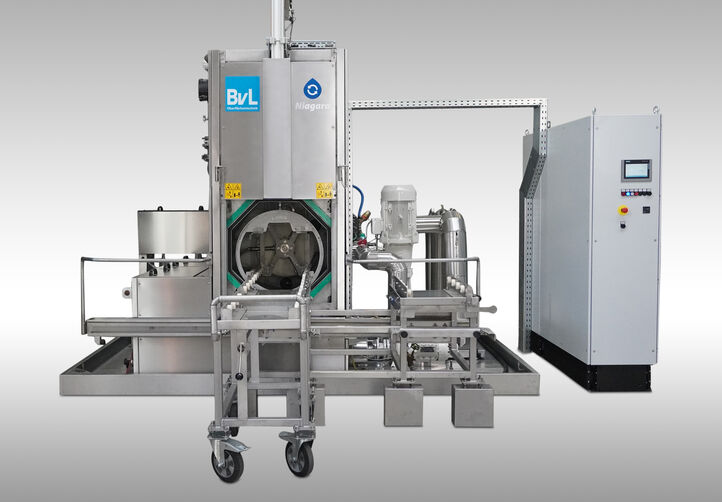
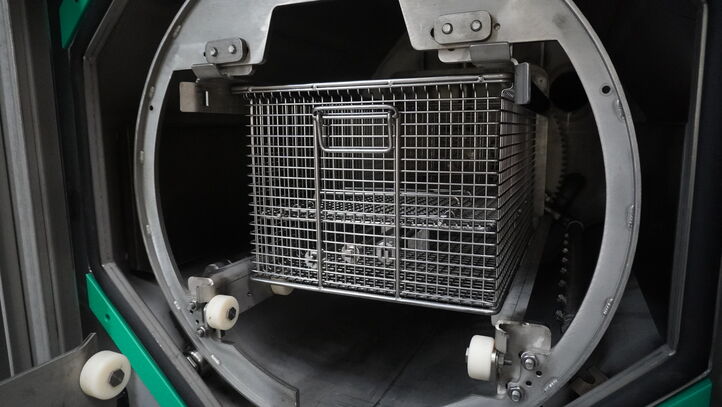