Increase productivity and clean different component sizes
Intelligent machine concepts allow for efficient cleaning of different component sizes simultaneously in the same system.
Correct positioning of the components is important for achieving a high cleaning quality. High-quality cleaning and drying results can only be obtained if the components are optimally aligned. Additional, specially aligned nozzle systems in the cleaning and drying process can reach difficult areas such as bores and blind holes, improving results and decreasing cycle times. For a broad product range with different component sizes, it is therefore important to have flexible, i.e. adjustable, component carriers in the cleaning system. This is the only way to ensure constant cleaning quality and secure accommodation of the components. To keep the entire process as efficient and economical as possible, it is crucial to use intelligent cleaning technology and innovative parts carrier systems.
Productivity increase and short set-up times with special technologies
“In the past year, we implemented a large number of interesting projects where different component sizes are cleaned simultaneously in a single system,” reports Bernhard Sievering, Managing Director and owner of BvL Oberflächentechnik GmbH. “We know that our customers can significantly increase their productivity if as many different component sizes as possible can be cleaned in the same machine at the same time. That leads to a higher throughput and more efficient processes in production. Set-up times are another aspect that is important to many of our customers. Set-up times have to be reduced in the value chain. We have developed different solutions that can be flexibly adapted to the specific customer requirements and integrated so that different component sizes can be treated in the same system. This allows us to achieve a very high level of availability for our cleaning systems.”
Automatic cleaning of gear shafts with different lengths
For an automotive supplier, BvL configured the Yukon conveyor cleaning system with an automatically adjustable workpiece carrier for cleaning pre-assembled gear shafts with lengths between 400 and 600 mm. In this specific application, the integrated loader interface supplies the component information from the automation (the 2D gantry) to the cleaning system, so that an adjusted parts carrier is ready to accommodate the workpiece for reloading. This fully automated system allows for “chaotic loading”, without running the system empty or complicated format adjustments. Setup times are eliminated altogether. The complex assembly is cleaned in a continuous cycled process with different treatment stages and subsequent drying.
Cleaning of gearbox housings with different heights
For its factory in China, a German gear motor manufacturer required a solution for cleaning gearbox housings with different heights from 208 to 282 mm. For this application, the BvL NiagaraDFS basket cleaning system was equipped with an innovative basket cover in the washing chamber. For thorough all-around cleaning, the workpiece pallets rotate during the washing process. To ensure that the batches are securely fixed in place as they rotate during the washing process, despite their varying heights, the washing chamber was fitted with adjustable hold-down clamps that are automatically adapted to the height of each batch. The Libelle Product Control (sensor system for inline component detection), which was specially developed by BvL, detects the different heights and sends this information to the closing mechanism of the cover. This omits the complex formatting and conversion work and the system can even handle batches of just 1 product in a reliable, automated process. The shuttle drive is another feature of this cleaning system. The portal loading system transports the components on the pallets from the loading/unloading station to pre-cleaning, final cleaning and the external vacuum dryer in fully automatic operation. This achieves a short cycle time and high quantities. The cleaning process also includes a passivating stage (corrosion protection).
Effective cleaning of tail pipes in different sizes
An automotive supplier from Slovakia offers a wide range of tail pipes for passenger cars in different sizes, with high technical cleanliness requirements. The manufacturer uses the BvL Yukon system, with component carriers that were configured specifically for avoiding unsprayed areas. The component carriers can be easily adjusted during operation of the machine and are therefore highly flexible. The targeted external and internal cleaning of the tail pipes covered in oil and other substances is carried out in a continuous cycled high-pressure process with special cleaning nozzles. A special lance technology was developed for the drying zone to ensure thorough drying, with the lances specifically moving into the pipes.
“When planning a cleaning process, you have to look at the entire production sequence,” explains Bernhard Sievering. “The cleaning system has to be perfectly integrated into production flow.”
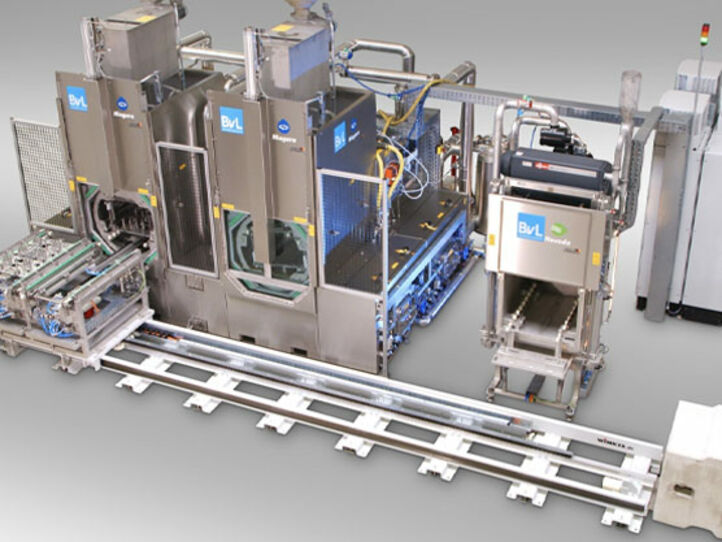
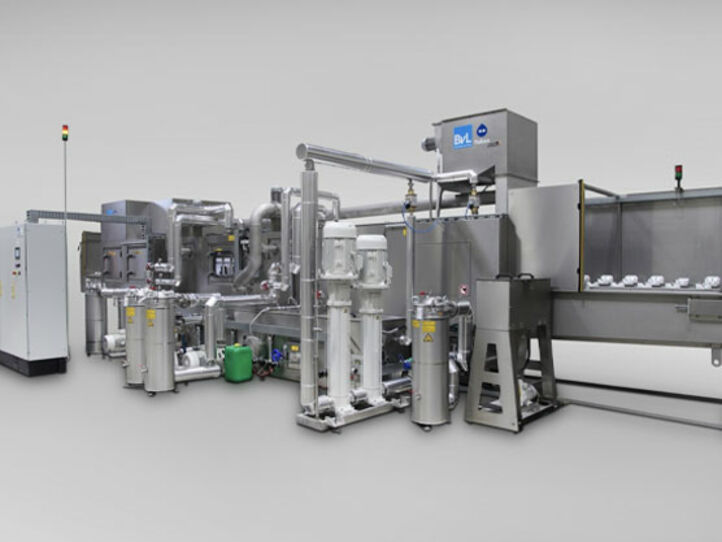
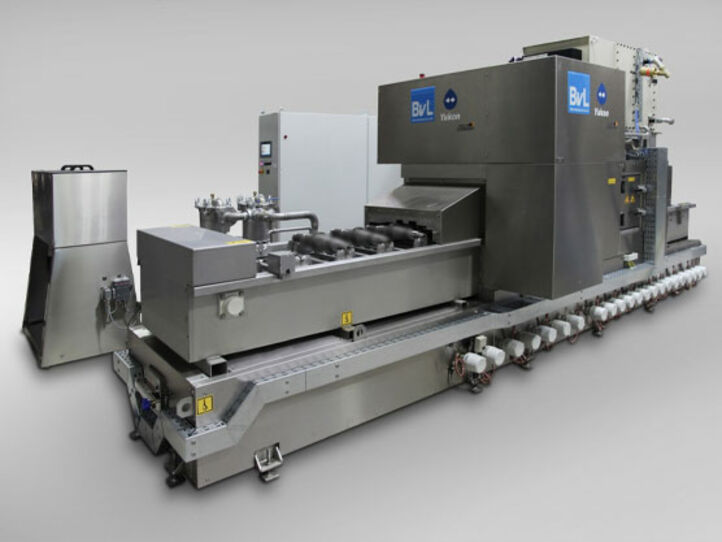