Cleaning different castings efficiently with high cycle times in one system
The modular structure of the three-station cleaning system allows users to react to changes in the cleaned goods, materials and volumes at any time.
A large supplier for vacuum pumps in Germany needed a new cleaning system for cleaning various pump castings made of gray-cast iron and aluminum. In addition to the stringent cleaning and drying requirements, a high throughput of components was also a key aspect. The customer selected the powerful OceanRW cleaning system from BvL Oberflächentechnik GmbH, which was customized to meet the requirements as a continuous cycled version. Different processing steps can be executed simultaneously thanks to the modular structure of the cleaning system. This now allows the vacuum pump manufacturer to clean different pump housings and their add-on components efficiently in the same system. To clean different part sizes in component baskets with different heights, the system detects the height of the current basket and automatically aligns the nozzle system accordingly.
High cleanliness requirements and corrosion protection for easy further processing
Before the pump components are installed, they have to be cleaned thoroughly to remove emulsions, oil, chips, aluminum flakes and adhering molding sand from the casting process. Dust, especially from sand blasting processes, also often adheres to areas that are difficult to access. The components have to be deburred and free from clamping chips. After cleaning, thorough drying of the components is required, including in the recessed blind holes, and a temporary corrosion protection has to be applied to allow for trouble-free further processing.
Increasing productivity and cleaning different components in the same system
The vacuum pump manufacturer can increase productivity significantly by cleaning many different component types and sizes in the same machine, which leads to a higher throughput and more efficient production processes. This crucial aspect also had to be considered in the planning of the new cleaning system. In addition, an existing basket and transport system used across different sites had to be compatible with the system to omit the complex handling tasks for removing the components from the baskets and clamping on workpiece carriers. This high efficiency gain during handling and the greater throughput ensured that the new system will pay for itself within a short operating period. The manufacturer found the expertise and good advice from the BvL team convincing. The modular structure of the BvL cleaning system now allows the owner to react to changes in the cleaned goods, materials and quantities at all times while the handling system makes the process efficient. But how does this cleaning system work?
Efficient cleaning and drying process with variable programs
The BvL cleaning system is equipped with a fully automated feed and discharge system. The components are transported in a component basket on a roller conveyor which is equipped with a special component scan and stop device for controlled parts feeding into the cleaning system. Potential collisions from protruding edges (which can theoretically occur due to incorrect loading) are reliably prevented by an intelligent scanning system. This prevents damage to the cleaning system caused by incorrect loading.
The components are cleaned and dried in a single work step. The three treatment chambers (washing/rinsing/drying) are run in parallel to achieve the best possible cycle time. Three washing baskets are always active at the same time and 6 to 8 baskets are processed per hour.
A lowering nozzle system in the washing chamber enables intensive cleaning with high pressure and a high volumetric flow, even for components with different heights. The star design of the nozzle system makes it very efficient and enables intensive treatment within very short processing times. A large number of different washing programs are available and can be freely selected in the machine controller for the BvL cleaning system.
The downstream rinsing chamber provides fine cleaning and pre-drying using integrated circulating air drying. This substantially reduces the moisture level in the third treatment chamber – the BvL Nevada vacuum drying – in advance.
Clever components in the cleaning system provide process reliability
Interface communication and remote service
BvL installed an OPC UA server and an Ethernet switch in the control cabinet so that all relevant system information can be communicated with ease. Direct support for system operation can also be provided via remote service.
Special filter technology
The filter elements are easy to replace. The Smart Cleaning consumption prediction for the bag filters displays the current level of contamination of the bag filter while also indicating to the operator exactly when the filter has to be changed. This makes predictive maintenance and keeping spare parts in stock as reliable and easy as possible, allowing the operator to efficiently integrate the filter change in the production process.
Monitoring the condition of the bath
The Libelle Fluid Control from BvL integrated into the system provides precise and fast evaluation of the bath quality. Every cleaning process requires a sufficiently pure cleaning medium. When the bath is depleted, sufficient cleaning results can no longer be achieved. The operator of the cleaning system therefore has to be aware of the condition of the bath to ensure constant component cleanliness. Libelle Fluid Control permanently measures the condition of the bath. The resulting data are output through the HMI. This reduces complex, cost-intensive residual dirt analyses to a minimum.
Energy-efficient cleaning
Improving the energy efficiency per component is an important aspect for the vacuum pump manufacturer. Various components of the BvL cleaning system are therefore insulated to greatly reduce thermal energy losses. Automatic switch-off functions for unused drives as well as standby functions during operation of the cleaning system, frequency-controlled pumps and energy-efficient motors and drives additionally support the energy efficiency.
Service and maintenance
Integration of an extensive maintenance platform that comprises all 3 treatment chambers allows maintenance and service work on components installed on the chamber roofs to be carried out very easily and quickly. Access steps additionally allow maintenance personnel to easily access the platform, even while carrying a tool case or other equipment.
BvL Oberflächentechnik will be exhibiting at the Euroguss exhibition in Nuremberg from 8 to 10 June in Hall 7, stand 414, providing information on application concepts and innovative solutions for cleaning castings from a variety of different industries – always customized for the individual requirements. Washing trials with original components can be carried out at the in-house technology center in Emsbüren.
Contact:
BvL Oberflächentechnik GmbH
Grenzstr. 16
48488 Emsbüren
Tel.: 05903 951-60
Fax: 05903 951-90
info@bvl-group.de
www.bvl-group.de
Press release:
Christine Brühöfner
Marketing
Tel.: 05903 951-509
Fax: 05903 951-90
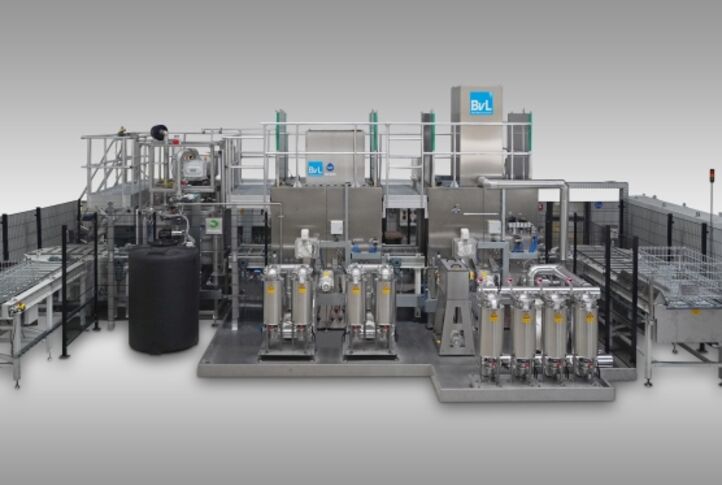
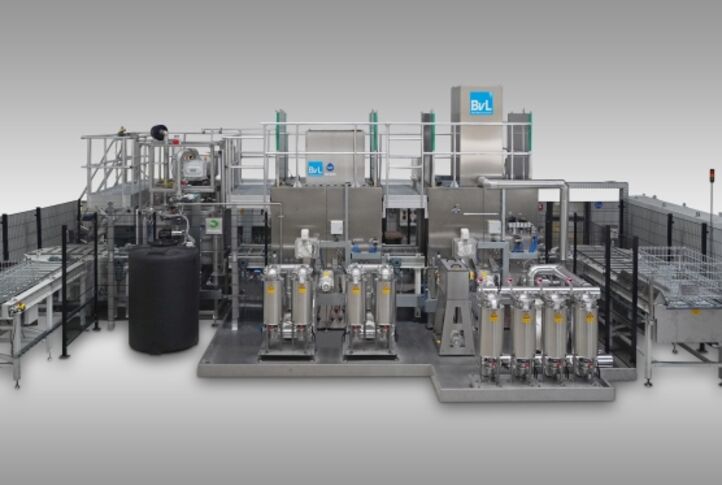
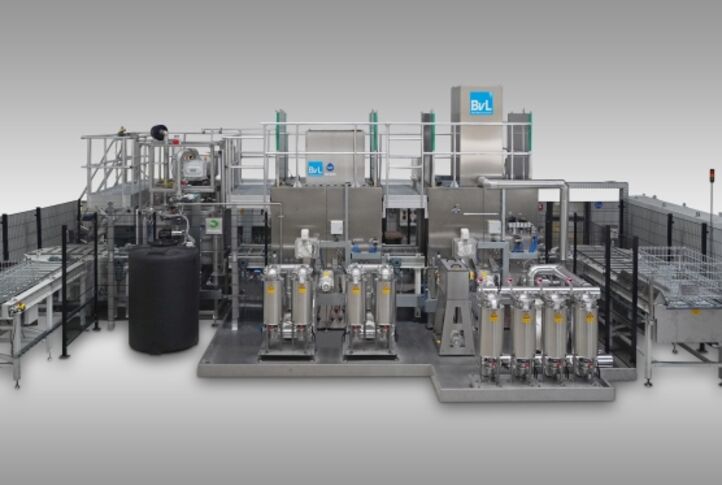
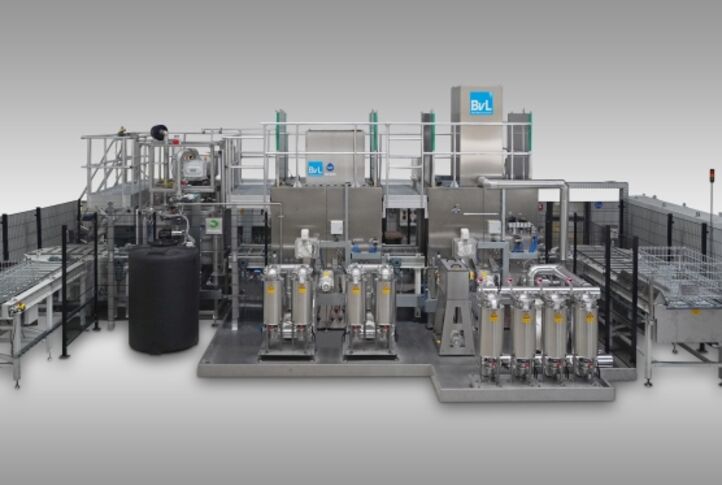
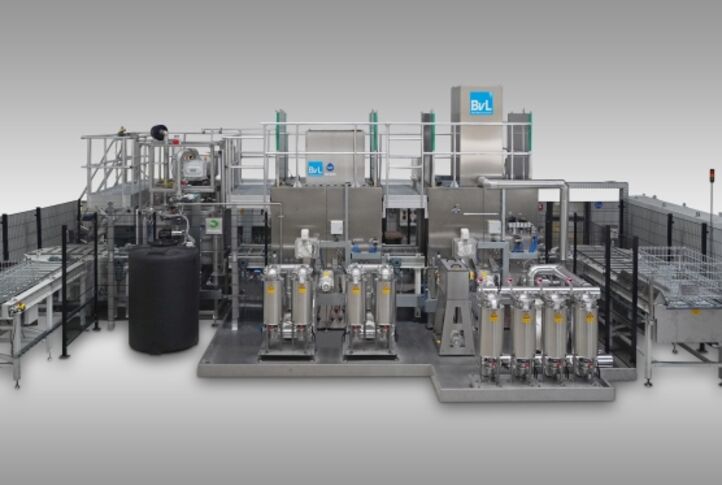
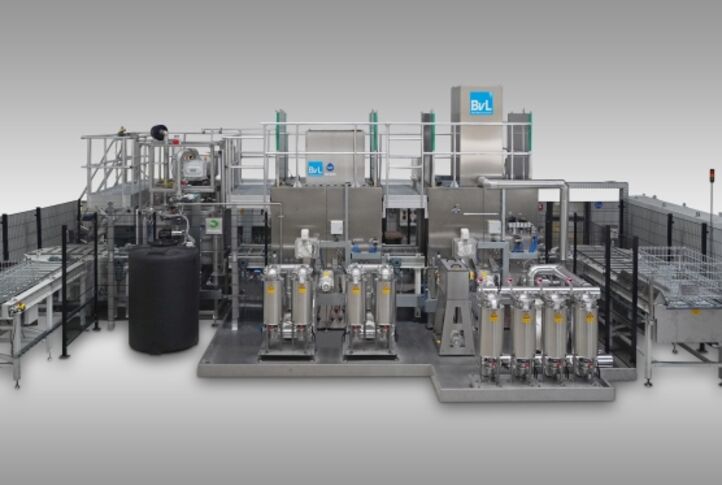